Event Highlights
Detailed Agenda Coming Soon
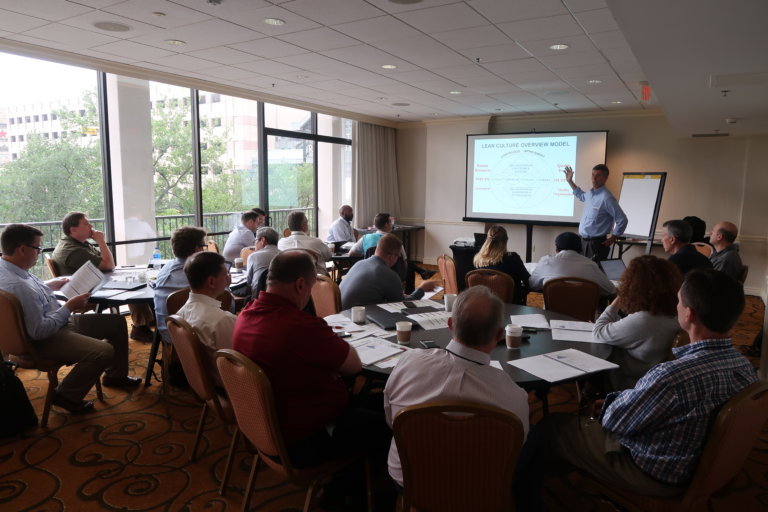
- Introduction to “True North” principles – mission, values and vision
- Philosophy and beliefs
- Company Vision & Strategy (Hoshin)
- Roles and Responsibilities for each Level
- Group Exercise - Servant Leadership in action
- Identify “Current State” of your organization’s Lean culture and specify Gaps in relation to the foundations of Daily Management
- Introduce Value Stream Organization and Management Structure
- Discuss the role of 5-S, Standardization, Training Methods, and Visualization
- Group Exercise - Continuous improvement
- Define the “Quality People Value Stream” – Attract, Select, On-Board and Engage
- Develop Lean Leader Standardized Work
- Learn firsthand from the experience of a former Toyota Team Member / Team Leader / Group Leader / Assistant General Manager
- Translate strategic direction into daily practices through Management Development Systems
- Structure Value-Added Level Daily Huddles
- Develop Systematic Problem Solving at all levels
- Create systems of Idea Implementation and Escalation & Problem Solving Teams
- Link Performance Management, Evaluation, and Company Performance
- Define Leadership Follow Through – Discipline, Accountability and PDCA
4P Workshop with Mike Hoseus
Delivered globally to executives from companies such as Nike, Philips, Coca-Cola, Pepsi-co, John Deere, BAE Systems, REI Outdoor
The 4P Workshop concludes with a Strategy Planning Session to help you transform your learning into an action plan. You'll identify where specific strategies can be applied to create a high-performance culture, develop action points to apply, and discuss how to communicate the vision and engage your organization.
Hear Mike explain more about the "Toyota Culture":
Working for Toyota
People Development
Audio Credit: Lean Frontiers
Learning Sites
Toyota Motor Manufacturing Kentucky
1001 Cherry Blossom Way, Georgetown, KY 40324
Explore one of America’s most advanced Manufacturing facilities with an in-depth tour of the factory floor in Toyota’s largest plant globally.
After the tour will be a group debrief:
- Group Observations and Question & Answer Session
- Learn from Mike Hoseus’ unique perspective as a former corporate leader for 13 years at the plant as Assistant General Manager in Human Resources and Manufacturing
- Group Discussion comparing different elements of Toyota’s engaged workforce and their culture of continuous improvement
Best Practice Sites TBD.
Woodford Reserve
Distillery Tour
Take a tour of the Woodford Reserve Distillery, one of the oldest distilleries in Kentucky. Woodford Reserve is a brand of premium small batch Kentucky straight bourbon whiskey produced in Woodford County, Kentucky, by the Brown-Forman Corporation.
For more information about the distillery, visit www.woodfordreserve.com
Testimonials
1
I have earned two engineering degrees and an MBA in finance over the course of my career. I have gone through 2 Lean certifications and I am a Six Sigma Black Belt… In all those courses the human element and the culture, which I know is foundational, was briefly glazed over. You guys have the “secret sauce” to true Lean deployment.
16
This is a real “where the rubber meets the road” learning experience. Highly suggested.
38
Absolutely amazing! Coming in I knew the technical side of TPS being in the Toyota family for 15 years but understanding the purpose, why and how to deploy was really eye opening for me. Really one of the best training I have ever received.
7
I am leaving the course energized to make a difference in my organization.
18
As an individual starting on my lean journey, the learning experience has been invaluable. I’m excited to start my journey with these principles as my foundation. Thank you!
39
This course was great in helping me as a new Supervisor understand the basics of the Lean principles and how to effectively apply the tools learned. I definitely recommend taking this course no matter your experience level.
40
I have been to many events during my career, and I can say with certainty that this is the best and most helpful Lean Manufacturing Event I have been part of. I highly recommended to any professional from any industry and to entire groups or teams, if possible.
37
Mike is an engaging Lean leader with real world experience at many levels within the Toyota organization. His practical knowledge and engaging style drives home the points presented in a way that sticks with the team. Great content presented by an outstanding teacher and relevant to any industry.
34
The experiences and sharing from Mike really helped me to challenge my baseline assumptions about how I think my organisation should function. I am returning to work re-motivated to support my teams and create the problem solving skills that we all want to see.
32
Great experience! Very informative, hands-on seminar. Activities to understand and apply principles covered in lectures. Mike is very engaging and open to questions and feedback. Met great people from other industries and was able to learn from them and relate to their problem-solving. Mike takes into consideration specific topics the group wants to cover or situations they would like to address and tailors the course to the needs of the attendees.
35
Meeting other practitioners, sharing experience, and going to see with the tours were important elements that made this course high-value for me. Mike brought many key concepts and lessons together that showed how true experts like him apply the Toyota Culture to create daily improvement practices which is the most valuable investment for any organization.
19
This course offers an abundance of learning and growth opportunities on an organizational level, as well as on the individual level.
Detailed Event Agenda We are pleased to offer a blend of learning experiences
Monday, April 22nd | |
---|---|
12:30pm Registration * |
|
1:00pm 4P Workshop (Part 1) with Mike Hoseus 4P Workshop |
|
5:00pm Networking Mixer |
|
6:00pm Group Dinner Downtown San Antonio |
|
* Please plan to arrive at the San Antonio Marriott Riverwalk no later than 12:30pm for registration. |
Tuesday, April 23rd | |
---|---|
8:00am Depart hotel |
|
9:00am Toyota Texas Tour Toyota Texas Tour |
|
12:00pm Lunch |
|
1:00pm 4P Workshop (Parts 2 & 3) with Mike Hoseus 4P Workshop |
|
5:00pm Networking Mixer |
Wednesday, April 24th | |
---|---|
8:00am 4P Workshop (Part 4) with Mike Hoseus 4P Workshop |
|
12:00pm Lunch |
|
1:00pm SWRI Visit & Masterclass * SWRI Visit & Masterclass |
|
4:00pm Debrief & End |
|
* For out-of-town participants, our final visit on Wednesday afternoon is located less than 20 minutes away from San Antonio International Airport (SAT). |