FocusIn is a knowledge exchange among senior executives and organization leaders in Operations, Sales, Human Resources, and Learning & Development across varying industries looking to seed and foster best-practices in their own roles and environments.
How can manufacturing plants benefit from Lean Management and Operational Excellence?
Lean Management and Operational Excellence are all about continuously improving processes, with a core focus on keeping people and purpose at the center of all operations. There’s a reason why Lean has become the leading organizational methodology across industries—that is, because of its emphasis on core values positive impact on overall company performance, the Lean method is universally beneficial. On the most basic level, implementing Lean improves organizational efficiency, increases customer satisfaction, and reduces waste and costs. But the benefits of Lean extend beyond your company’s bottom line. Lean organizations also experience higher levels of employee engagement, stronger management principles, better project visibility, and increased team morale.
What is Lean Management?
Lean Management is all about creating systems of continuous improvement while maintaining respect for people at the center of all operations. The origins of Lean date back to the Toyota Production System (TPS) of the twentieth century. Centered on People, Processes, and Purpose, the Lean Method is a practical and cultural tool for maximizing value and reducing waste across the organization.
What is the difference between Lean Management and Operational Excellence?
In our perspective, Lean Management is the reason to be of Leadership. In other words, it is a philosophy of how you foster continuous improvement and build skills to become a more resilient organization. Operational Excellence is the process of taking that philosophy and putting it to action by using a set of tried and tested tools.
How can I build a Lean Culture for my organization?
At the heart of every successful organization is a strong, people and process-focused culture, but building Lean Culture doesn’t happen overnight. The journey to establishing a company culture of continuous improvement requires serious effort by every leader in the organization. Moreover, because culture is so heavily engrained into everything an organization is done, leaders just beginning their Lean journeys often struggle to transform their organization’s culture for the better.
There are many barriers to changing organizational culture and behaviors, including a fragmented workforce, poor communication practices, or low employee engagement. Despite the challenges associated with making this sort of cultural change, the benefits are worth it. Each step along the process is a unique opportunity to learn and strengthen your people and culture.
How can I assess my company to improve manufacturing ROI?
As any organizational leader can tell you, a clear and honest assessment of processes is the first step in any sort of improvement exercise. With a proper and thorough organizational assessment, leaders are able to identify problem areas and highlight best practices.
An objective, third-party organizational assessment is the best way to maximize process ROI. Not only can an independent assessment help you evaluate your processes on an intrinsic level, but it can also allow you to identify waste and inefficiencies by benchmarking your results against industry competitors and other best-practice organizations.
How can my company improve by benchmarking?
Benchmarking is the process of comparing your company’s performance and practices with other organizations in order to highlight best practices and promote their adoption
Benchmarking is a critical exercise for many reasons, the first of which being that no company operates in a vacuum. Even if your organization is the best-in-class industry leader, there is always something that can be improved, and looking outwards to other organizations is a great way to maintain a competitive advantage. By maintaining an outward focus on industry standards and consumer expectations, business leaders can have a better understanding of their company’s own position in the market.
While benchmarking is a great way to look for solutions to a specific problem your organization is facing, it is also a useful method for identifying potential areas for improvement that perhaps were not even on your radar. By building relationships with other industry leaders and familiarizing yourself with their processes and best practices, you can discover better ways to do things and identify problems that you previously did not even recognize as being problems or inefficiencies
What are the different Operational Excellence methodologies?
- Lean Management
- Six Sigma
- Kaizen
- Shingo
- Agile
- Total Quality Management
- Theory of Constraints
All of these frameworks have their own distinct language and method of application, however what is consistent is the principles around building effective communication, identifying problems, and following a structured process to drive improvement.
Previous Participant Companies

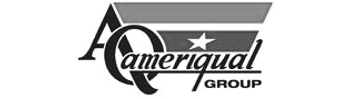
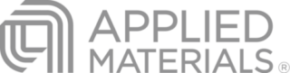

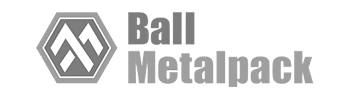
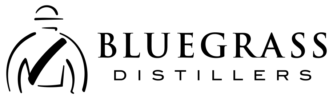
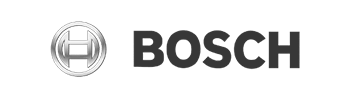
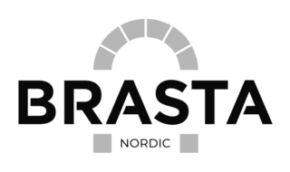
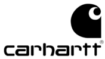
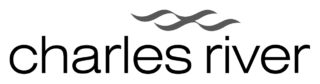
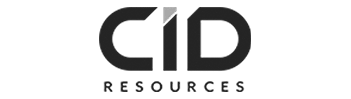
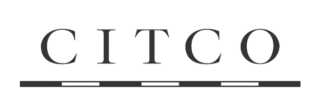
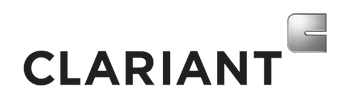
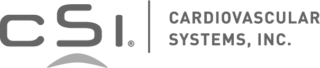
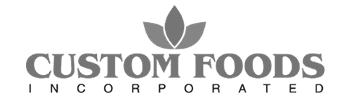
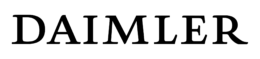
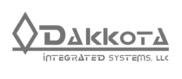
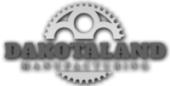
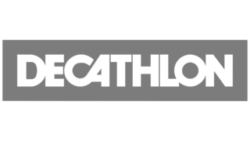
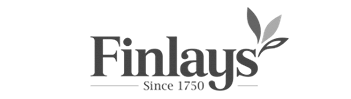

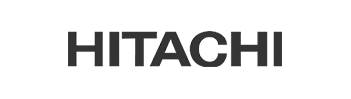
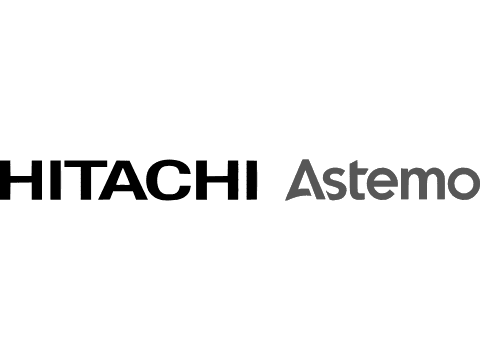
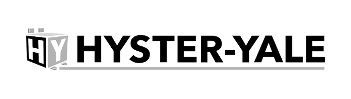
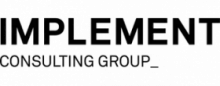
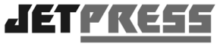
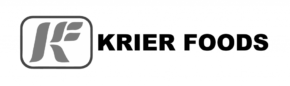
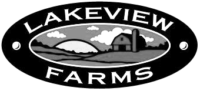
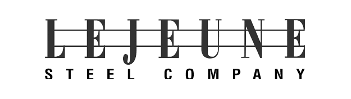
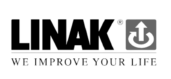
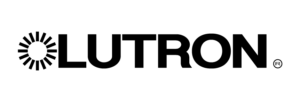
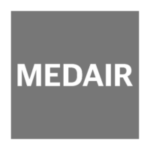
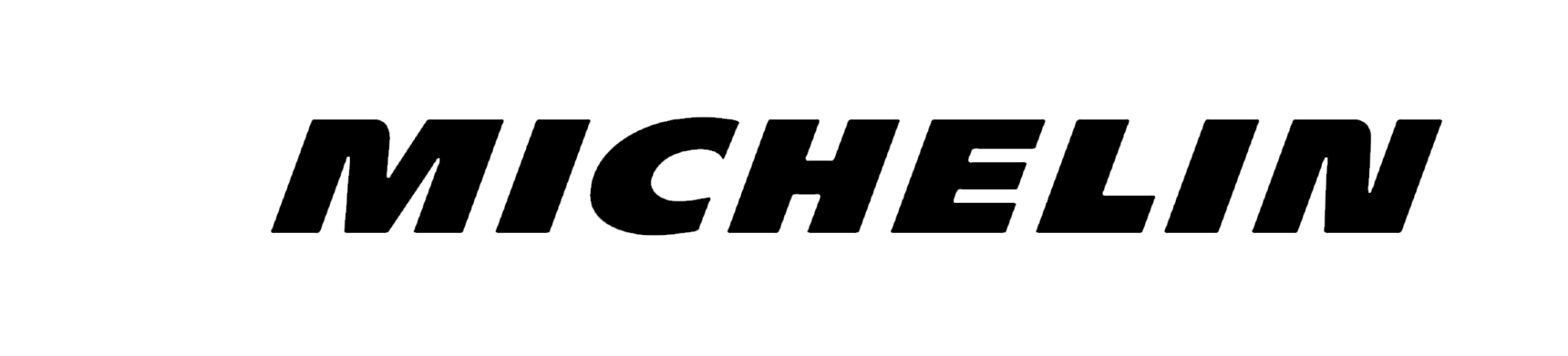
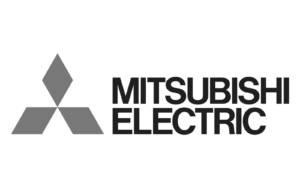
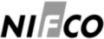
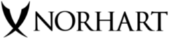
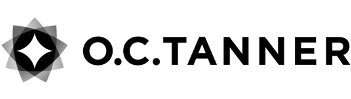


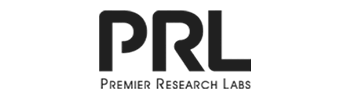
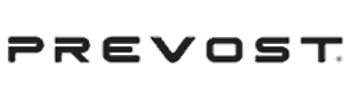
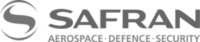
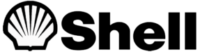
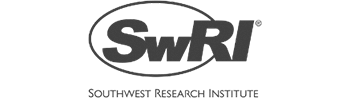
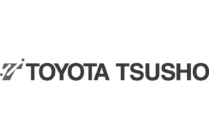
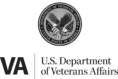
- Ameriqual Group
- Ball Metalpack
- Bosch
- CH Guenther & Son
- CID Resources
- Clariant
- Custom Foods
- Finlays
- Hitachi
- Humble House Foods
- Hyster-Yale
- Lejeune Steel Company
- O.C. Tanner
- Premier Research Labs
- Prevost
- Southwest Research Institute